In the field of mechanical assembly, discussions about the friction coefficient have always been a hot topic. Typically, a high friction coefficient is widely used because it can enhance the anti-loosening performance of bolts and reduce torque decay, thereby ensuring connection stability. However, German car manufacturers have a preference for low friction coefficients in bolt tightening processes, which is backed by profound principles and significant advantages.
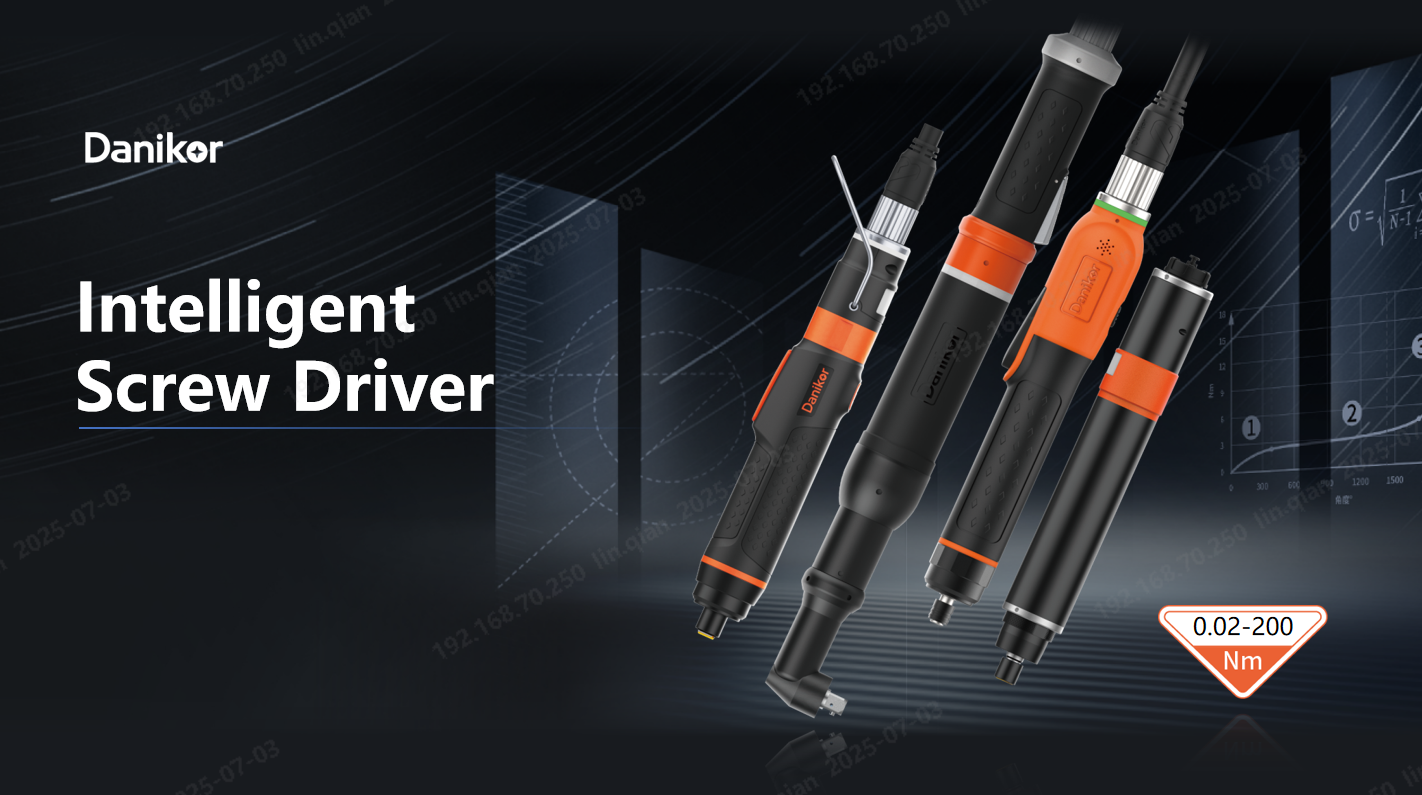
From the mechanical perspective of bolt tightening, according to the clamping force calculation formula, under the same tightening torque, the lower the friction coefficient, the greater the preload generated by the bolt. This means that the connection can withstand greater external forces, providing a stronger clamping effect and reducing the likelihood of loosening under various complex conditions during vehicle operation, fundamentally enhancing connection reliability. Moreover, a low friction coefficient reduces the torque required during the tightening process. For automotive manufacturers, this directly means that they can use tightening equipment with a lower range to complete assembly tasks. Equipment with a lower range is often more cost-effective, reducing acquisition costs, while also offering higher precision, better meeting the stringent assembly accuracy requirements of German cars. This helps companies optimize their production cost structure while ensuring product quality.
Another crucial point is that a low friction coefficient can effectively prevent the occurrence of stick-slip phenomena. Stick-slip can cause sudden changes in torque during tightening or operation, leading to noise and vibration. Under the German car philosophy that emphasizes driving and riding quality and comfort, reducing noise and vibration is an important aspect of enhancing user experience. A low friction coefficient makes the tightening process smoother and quieter, fundamentally reducing noise and vibration issues caused by stick-slip, allowing the vehicle to maintain higher comfort and stability during operation.
In this industry context, Danikor's intelligent screwdriver, with its reliable performance, has become the choice of automotive manufacturers and many other enterprises pursuing high-precision assembly. Danikor's intelligent screwdriver uses advanced sensor technology and high-precision control systems to accurately control tightening torque, ensuring that each tightening operation meets process requirements. Its intelligent control system can quickly adjust tightening parameters according to different bolt specifications and assembly needs, adapting to the tightening process with a low friction coefficient. Additionally, it features real-time monitoring capabilities, providing immediate feedback on torque changes during tightening. In case of any abnormalities, it can issue an alarm and stop the operation, effectively preventing connection issues caused by excessive or insufficient torque, ensuring the stability of assembly quality.
Moreover, Danikor's intelligent screwdriver is designed with ergonomics in mind, featuring a simple and intuitive operating interface that significantly improves production efficiency. Strict quality control measures also ensure the durability and reliability of the equipment in high-intensity, high-frequency industrial production environments.
The advantages of a low friction coefficient in bolt tightening are evident. Danikor's intelligent screwdriver, with its intelligent control, monitoring, and reliable performance, provides high-quality tightening solutions for the automotive manufacturing and other mechanical assembly industries. It helps companies continuously improve product quality and production efficiency, meeting the market's demand for high-quality products.