What Precautions Should Be Taken for Screw Feeding and Tightening Error-Proofing?
In modern manufacturing, tightening operations are an essential part of the assembly process for many products. However, errors that can occur during tightening, such as floating high, stripped threads, and repeated tightening, can have a serious impact on product quality and reliability. Therefore, error-proofing in tightening should not rely solely on standardizing employee operations but should be considered and optimized from the perspective of the entire production process.
I. Incoming Material Control: The First Line of Defense for Error-Proofing
The first step in tightening error-proofing is to strengthen incoming material control. Only by ensuring that the materials entering the tightening system meet the standards can we fundamentally avoid tightening errors caused by material issues. In the incoming material stage, methods such as length detection of screws can be used to strictly screen fasteners like screws. Danikor's screw feeder plays a significant role in this stage. It not only quickly conveys screws but also automatically identifies and screens out screws that do not meet specifications through its built-in detection mechanism, ensuring that every screw entering the tightening system meets the standard. This approach of controlling material quality at the source lays a solid foundation for subsequent tightening operations.
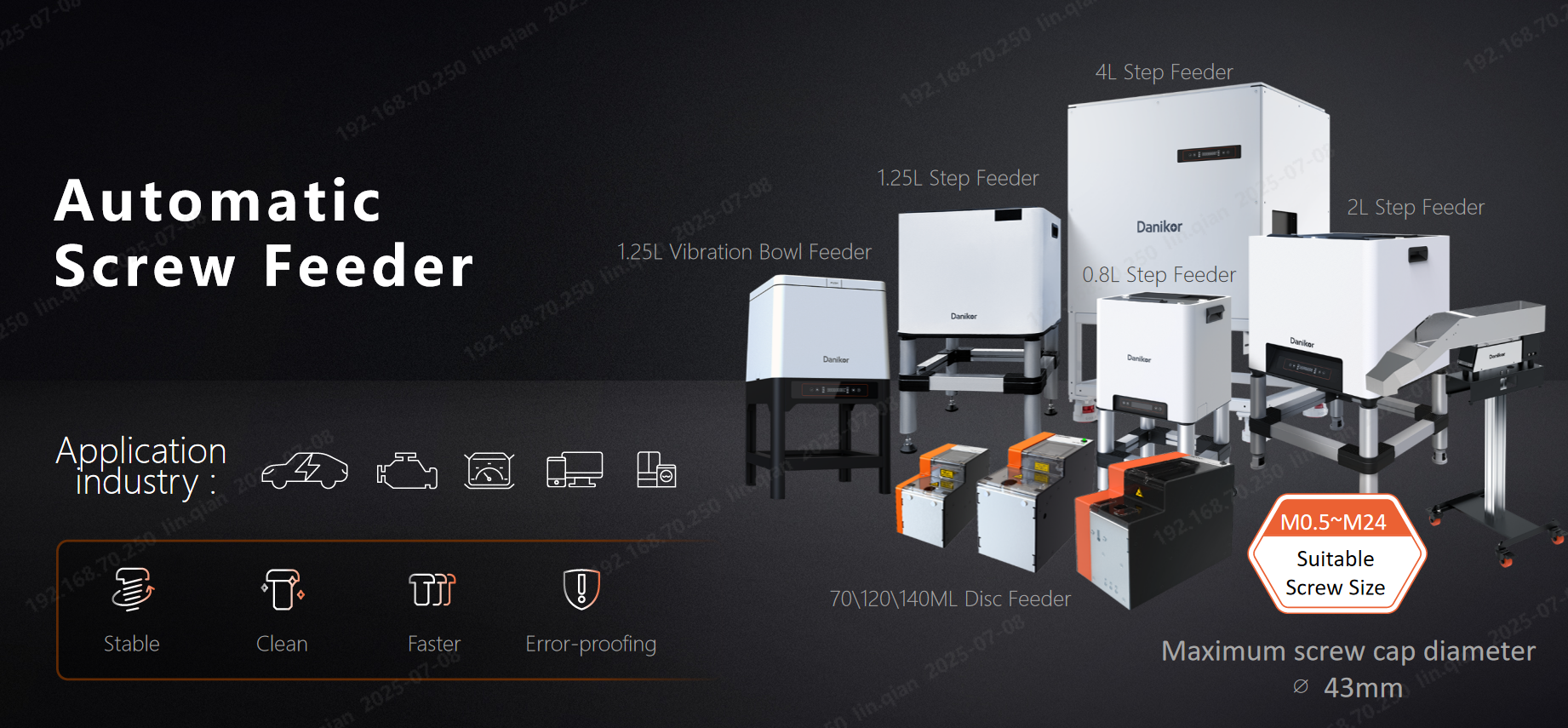
II. Equipment Control: The Combination of High Precision and Intelligence
Equipment control is a key link in tightening error-proofing. Choosing the right tightening tool is crucial. Danikor's intelligent screwdriver, with its high-precision torque control and multiple monitoring strategies, can effectively identify abnormal situations during the tightening process. During tightening, Danikor's intelligent screwdriver can accurately control torque, ensuring that every screw reaches the required tightening force as designed. It also has multiple monitoring functions that can monitor floating high, stripped threads, repeated tightening, and other issues in real-time. Once an abnormal situation is detected, the screwdriver will immediately issue an alarm and stop the operation, thereby avoiding quality issues caused by tightening errors.
In addition, Danikor's intelligent screwdriver also has data collection and storage functions. It can record the tightening data and curves of each screw, providing strong support for subsequent quality tracing and analysis. These data can not only help production managers promptly identify potential quality issues but also provide a basis for optimizing production processes.
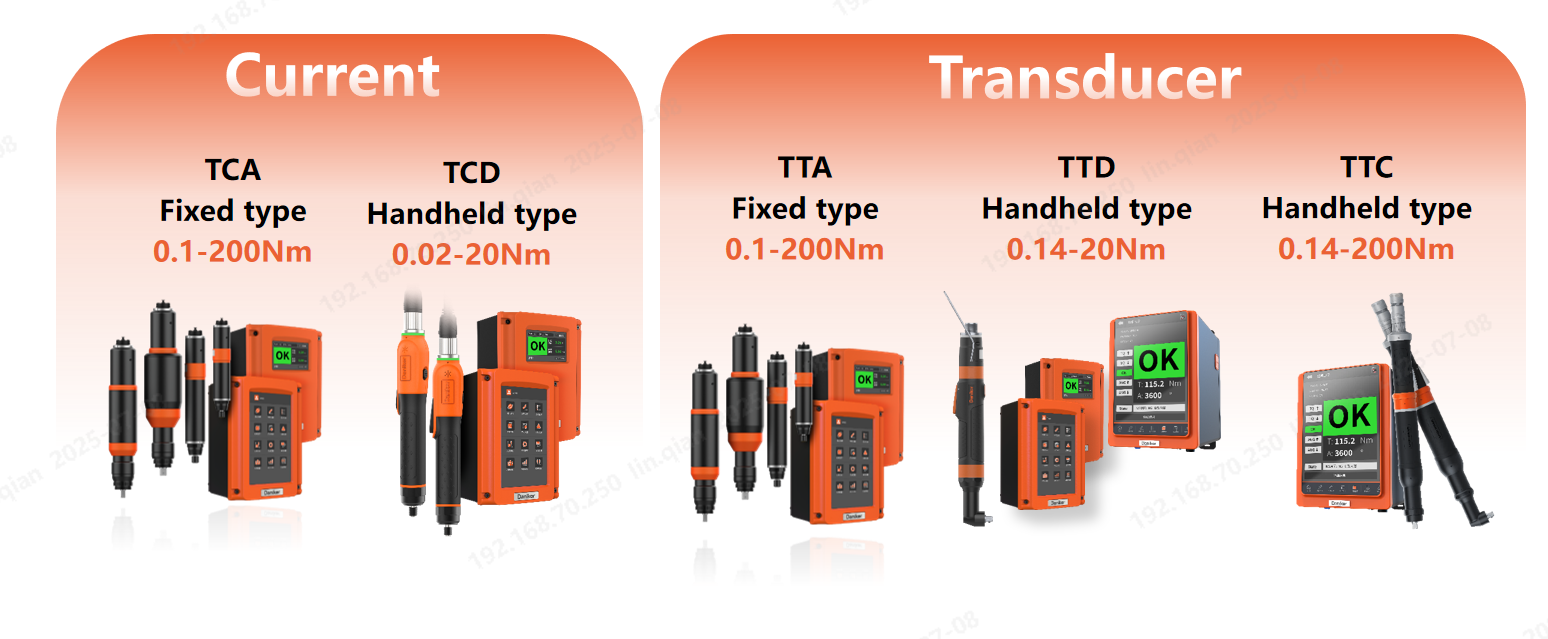
III. Control of Assembly Position and Sequence
In addition to material and equipment control, the accuracy of assembly position and sequence is also an important aspect of tightening error-proofing. In actual production, operators may cause assembly position errors or chaotic tightening sequence due to negligence or other reasons. To address this issue, positioning levers and position encoders can be used in combination. The positioning lever ensures that the tightening tool operates in the correct position, while the position encoder monitors the assembly position and sequence in real-time. If an error is detected, the system will immediately issue an alarm and prompt the operator to correct it. This technical assistance to operators can effectively prevent tightening issues caused by assembly position or sequence errors, even if the operator is not particularly attentive.
In modern manufacturing, tightening error-proofing is an important link to ensure product quality and reliability. By strengthening material control, selecting the right equipment, and optimizing assembly positions and sequences, tightening errors that may occur during the process can be effectively avoided. Danikor's screw feeder and intelligent screwdriver play an important role in this process, providing strong support for quality control in production.